Damaris Davis bought a 3D printer thinking she’d start a few small projects in her free time, but her twelve-year-old daughter had other plans. Inspired by a recent cover of Make Magazine, she wanted to build a humanoid. “And so that’s what she did one summer,” said Damaris. “It blew my mind.”
But Damaris is no stranger to this behavior. Proud second in three generations of makers, Damaris also used her father’s engineering tools to create while growing up – clubhouse parts out of wooden planks, miniature speakers via circuit from the electrical kit, maze games on outdated desktops her father salvaged from work.
Her daughter’s humanoid was a welcome addition to the extended Davis family, a community of robots that now keep Damaris company in her home office. Like her father, she keeps her workspace open for her children’s use. After all, his generosity is what sparked her trifold interest in hardware, software, and electronics – the trinity of skills that inform her career today as a development engineer in HDD R&D.
Since those early days acquainting herself with her dad’s toolkit, Damaris has earned multiple patents for her innovations to the Advanced Fine Lapping machine. Her improvements help manufacture the read and write heads responsible for vast amounts of the world’s data.
Refining this technology has required Damaris to continuously up her own problem-solving game throughout her 20-year career at Western Digital. Thankfully, she’s always been game for a challenge.
In high school, Damaris joined the Science Olympiad – one of the U.S.’s premier competitions for the sciences – because she liked making Rube Goldberg machines. She stayed because she liked the people even more. Each year they brought a larger, more sophisticated Rube Goldberg machine to the Olympiad. Senior year they pulled out all the stops with the Big Green Helix Machine, which contained almost a cubic meter of chain reactions running the gamut of engineering disciplines.
While her predilection for hands-on work made mechanical engineering the obvious choice for her college major, she still performed well in her programming and electronics classes at UC Berkeley. She saw a 3D printer for the first time in the basement of the mechanical engineering building, where she spent late nights programming robot arms.
Damaris began exploring her diverse interests through a series of internships at IBM beginning in 1997. She worked with robots on the automation line in the Great Oaks facility before moving to run experiments in the materials lab. Next was data analysis for manufacturing, until she ultimately wound up in IBM’s Almaden research facility helping a team invent a new kind of machine.
The Mirreon machine would manufacture the read and write heads of hard disk drives. This was a uniquely difficult process to contain and systematize given the nature of read and write head technology, magnets that rest a few atoms above a platter spinning roughly 10,000 times every minute – a process Damaris compares to a jet engine flying a centimeter off the ground. Always up for a challenge, she was an excellent fit. IBM soon hired her to work full-time as a development engineer.
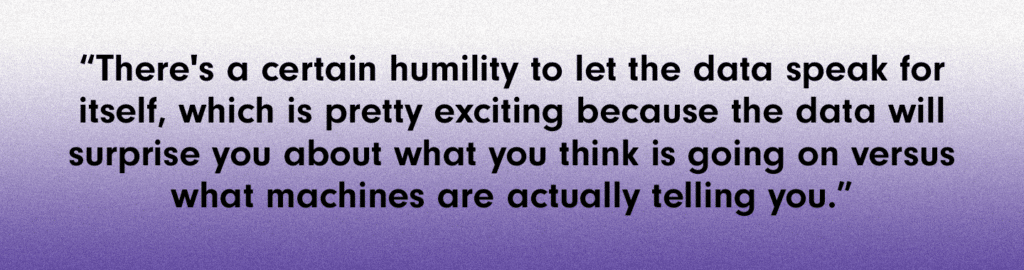
As the Mirreon machine matured and began its term at a factory in Guadalajara, Mexico, Damaris’s work on the project shifted to analyzing its data remotely. IBM was an early adopter of big data collection. “Since pulling data has been around, [IBM was] doing it, while other companies may have been using spreadsheets to keep track of what was going on,” she said.
Damaris belongs to the first generation of engineers to integrate big data into the engineering process. Her team’s success with the Mirreon and its heir, the Advanced Fine Lapping (AFL) machine, helped cement big data’s importance in the Fourth Industrial Revolution.
Lessons from big data have empowered the AFL machine to outlast the Mirreon several times over, advancing through four generations. The team developed the first three generations along the same tack, improving reader dimensional control to the precision of one nanometer by processing about 60 parts at a time using a multiple pressure zone to control the reader. But most of Damaris’s patents lie with the fourth-generation AFL technology.
For this iteration, the team embraced an entirely different approach. This time, they introduced a second axis of control to the machine, enabling it to manipulate two axes per module, literally scaling production into a whole new dimension. This exponential leap in technology has become a capstone of Damaris’s career.
She credits much of her problem-solving success to the Six Sigma method, a data-driven method for improving manufacturing processes that focuses on outlining the problem at hand to identify every possible variable at play. “Sometimes people see there’s a problem and they just reach for the simplest solution,” said Damaris. “Versus understanding what the problem really is and trying to find its root cause.”
While locating the root cause is easier said than done, it can result in the most satisfying work. “Once you have the details and line them up like a puzzle, it gets exciting to see that if the data is consistent, it will lead you to the right answer without having to jump to the conclusion.”
When an AFL machine misfires in the Philippines, Damaris searches the numbers from halfway around the world. It still surprises her how quickly she can spot the fault from data alone. Though the time difference between California and the Philippines can result in late-night calls, collaborating to solve problems is its own reward.