Dr. Anna Ploszajski: Explaining the Future of Materials
Dr. Anna Ploszajski is an award-winning materials scientist, storyteller, and author. She blends craft-making and groundbreaking materials science research to help us understand our relationship to materials and how they impact our world.
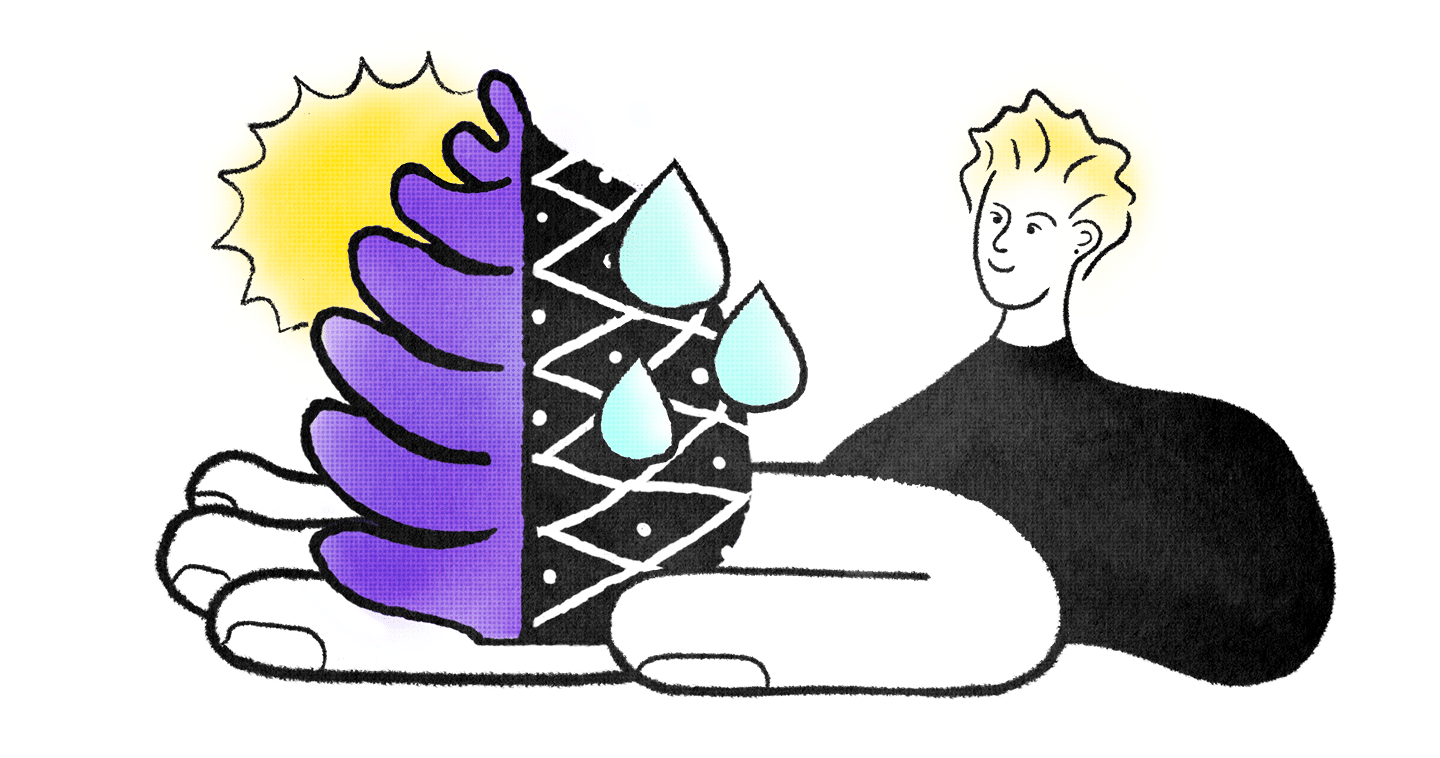
If you had to sum it up to its most simple elements, what is the story of materials science, and what does the next chapter hold?
Well, the story of materials science is the story of humanity, really. We measure progress by materials, right? The Stone Age, the Bronze Age, and Iron Age. So materials and our current technologies say everything about us, about what’s important to us.
At the same time, all of our stuff comes at a cost—an impact on the planet. And what are we willing to pay? So, I think that the difference for future materials will be between a circular material economy and not. A circular material economy is sort of counter to how a lot of our material world has progressed so far, because we’ve been striving for increased complexity. But a more sophisticated approach will be in engineering elegant and efficient uses of materials and how we deploy them.
When considering these future materials, what properties are you looking for? Is it about biodegradability, or is it something else?
We have to look at the full life cycle—manufacturing, energy use, end of life, everything. First, I would look for raw materials that come from sustainable or renewable sources. Then, it’s about materials that don’t require a lot of heat, chemicals, or energy to produce, and materials that don’t create a waste stream that we don’t know what to do with.
One problem that we often have with plastics is that tiny fibers of polymer textiles can become airborne. We hear a lot these days about microplastics in the environment and in our bodies, and that has to do with the stability of the material over its lifetime.
So, the question of lifetime is really crucial. The packaging for produce, for example, might only need to last a couple of weeks from packaging to consumption. But the plastics we use to ship them last way longer. They will remain exactly the same for many years, potentially decades to come. That’s massively over-engineered for what I needed it to do.
“The story of materials science is the story of humanity.”
Speaking of plastics, you’ve previously talked about the challenges of recycling plastic. Why is it so difficult and could materials science herald a solution?
It’s such a multi-layered problem. Plastics are such a diverse family of materials, which is one of the reasons why they’ve had such a huge impact on our lives. It’s a category of material that is the most diverse if you think about the applications, forms, and the properties that you can make with it. So that’s the first problem: there are thousands of different types of plastics, and it’s difficult to generalize what we should do with them.
Then, some categories of plastics, like thermoplastics, can be melted down and reformed into other things, theoretically. But whenever you apply a chemical process or a heat process to a material, there’s always degradation and decay. That’s the second problem.
The third problem, as I see it, is a social problem. We can’t underestimate how much plastics have helped us; they have democratized medicine, and they have allowed food security for people around the world. The problem that we have, though, is with single-use plastics, and that we’re not willing to let go of that stuff, to change our behavior, or change how we’re using these materials.
So, it becomes a design problem, a social problem, a behavior problem, an expectation problem, and a consumer problem.
Your post-doctoral research focus was smart materials and creating a 4D manufacturing platform—what are these materials exactly?
Yeah! First, a smart material is a substance that responds to changes in its environment in a way that living matter sometimes does. For example, it might change shape if the sunlight falls on it, like the head of a sunflower would. These are called 4D materials, with the fourth dimension being time.
One of my favorite examples of smart materials is the pinecone. It has a simple structure of two layers of wood sort of bonded onto each other. When it gets wet, one side of the little spine expands more than the other and that causes it to bend over and close up. It’s a simple and ingenious design.
Similarly, instead of programming or creating robotic actuators, materials can inherently respond to their environment, like shrink or expand. Simple, self-deploying structures made from smart materials is something I see as making the leap from the lab to the practical.
Despite everything being made of something, materials science remains abstract. Your book, “Search for Meaning Through Making,” is about turning the abstract into the tangible. What did you discover?
One of the reasons why our field feels intangible is that what we, materials scientists, are so interested in is zooming in on the building blocks of matter. What we’re interested in is invisible. And that was my world—understanding materials on paper. It wasn’t until I watched a professional glass blower during my PhD that I realized I only knew a tiny proportion of the knowledge that humanity holds about materials. I had no idea how to practically do any of this stuff, like throw a pot on a potter’s wheel, glass blowing, or how to blacksmith. I had none of these skills, even though all of them had to do with materials.
Materials science itself only really became a discipline within the last 200 years, once we discovered atoms and understood how they can help explain material phenomena, like how atomic bonding can explain why steel is strong. But it stands on the shoulders of craftspeople and all of those folks who worked with materials. Our mastery of materials is actually centuries, millennia old.
What I learned from that was that our bodies of knowledge are separated by educational establishments, but we’re all very interested in the same thing. It really opened up my eyes to trying to understand and paint the fullest picture of materials that I could.
What materials would you say define this era, and what materials will describe the next?
It’s got to be silicon, isn’t it? I mean, this is the semiconductor era. We live in a digital age. Our modern lives would fall apart extraordinarily quickly if we clicked our fingers and there were no silicon semiconductors tomorrow. That being said, carbon is the thundercloud on the horizon. I’d be surprised if carbon doesn’t define the next age for us, certainly in terms of a turning point for humanity.
With that in mind, what I would like to see is a shift to simplicity. Rather than creating ever more complex devices and machines and objects that are impossible to repair, recycle, or do anything with after they break, can we find a way to return to simpler designs? Can we be more sophisticated by using fewer materials to achieve the same result?
If you think about our world, it would be pretty unrecognizable to even our grandparents, let alone to people further back in history. And yet, the crockery in our cupboards, the bricks that we build our houses out of, a lot of that would be recognizable by someone who lived a thousand years ago. And in a similar way, I think the future will look both familiar and new.