Dr. Carlijn Mulder: A Leading Scientist’s Take on Magnets
Dr. Carlijn Mulder is the Dutch scientist leading Niron Magnetics’ Magnet R&D department. She is taking the company’s breakthrough material out of the lab and into the world, hoping to reconcile technological progress with environmental sustainability.
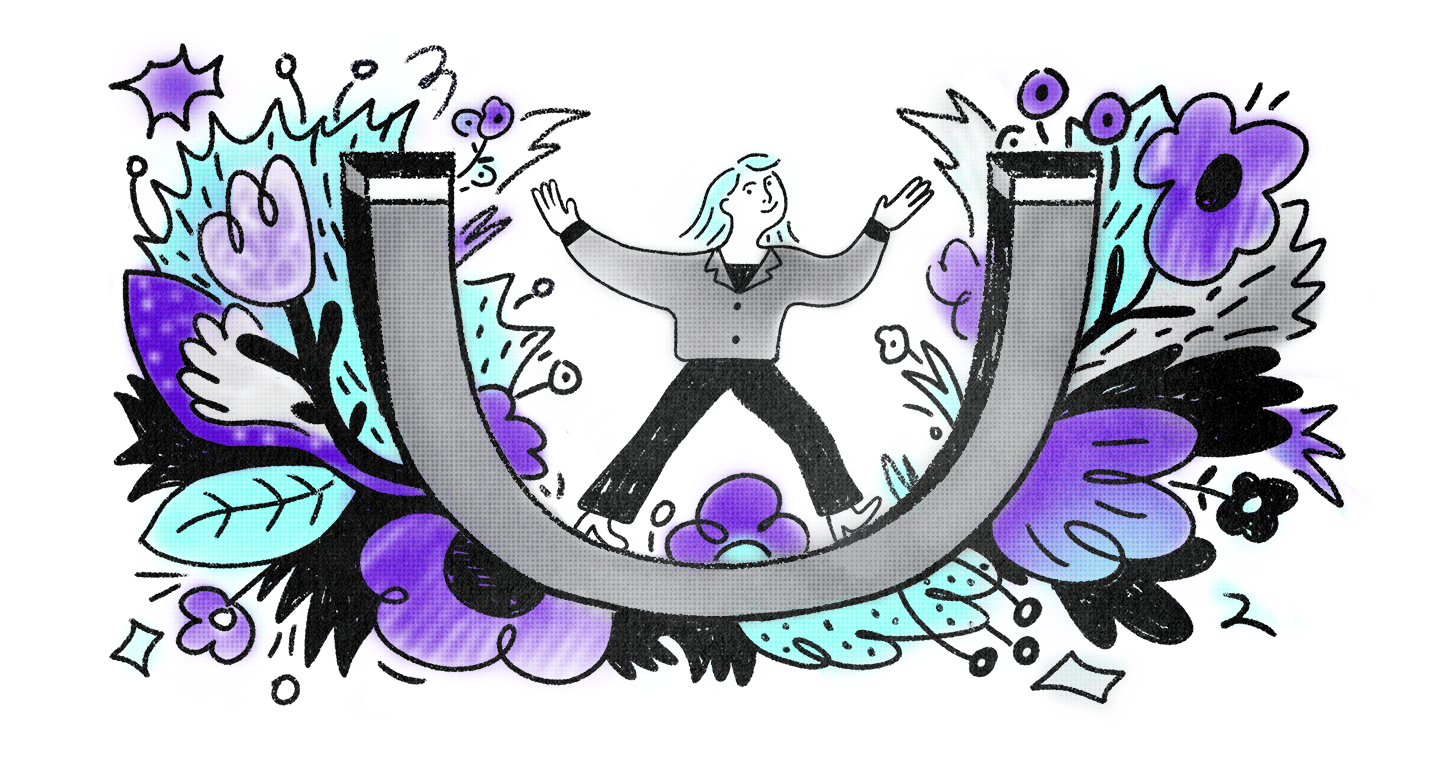
Human civilization has been defined by materials—the Stone Age, the Bronze Age, Iron Age. What materials do you think define this era, and which will describe the next?
In contrast to the ages mentioned before, I think we currently live in an era where, more than ever, we are controlling the microstructure of natural elements, placing all those atoms in the exact places we want. By deliberately engineering our materials at the nano-level we are unlocking and applying the physics that governs at the quantum scale. These materials properties allow us to develop devices that are unique compared to the earlier ages, like transistors, superconductors, LEDs, hard disk drives, and super-strong permanent magnets.
You’re doing this type of exciting materials engineering at Niron Magnetics. But it’s not just what you’re doing, it’s why you’re doing it. People aren’t necessarily aware of the environmental cost of extracting rare-earth metals that go into our countless devices. Can you tell us what is needed to make our devices possible?
The term “rare earth” is slightly confusing. I think the best way to think about it is that these elements aren’t rare in terms of the total amounts found in the Earth’s crust, but instead, they are typically found at very low concentrations. Moreover, the rare-earth elements are chemically quite similar to one another. This makes the isolation and refining process difficult, and it requires very harsh chemical treatments to extract them from the ore. Finally, often there are radioactive elements co-present with rare-earth elements that become part of the waste stream.
As a result of all this, to produce one ton of rare-earth elements, 2,000 tons of highly toxic waste is generated.
Is that intersection of environmental importance and impact behind Niron’s work and technology?
Absolutely. We don’t want to replace one “evil” with another, right? If we can manufacture these high-performance magnets with abundant materials, with a clean process, that’s going to be huge for the future we’re all pushing towards. We believe that the clean energy transition is necessary, but we have to be able to do that transition without creating other problems. That’s why we so strongly believe that our Clean Earth Magnet® is an important product to bring to the world.
A commercial high-performance Clean Earth Magnet has never been made before. What is it, exactly, and why is it so hard to do?
The α ″–Fe 16 N 2 phase of iron nitride, the material we use for Clean Earth Magnet, was first discovered in the 1950s. Yet scientists couldn’t wrap their heads around its underlying physics, and the experimental observation of its giant magnetization was controversial. It was Professor Jian-Ping Wang at the University of Minnesota who sank his teeth into the problem. In the 2010s, his work showed that it was possible to achieve that high level of magnetization, theoretically 50% higher than the rare-earth magnets, with iron nitride.
The biggest challenge, though, is how to manufacture it, reliably, in bulk. Our manufacturing method is nanoparticle-based. We start with a chemical precipitation process to produce our starting raw material, iron oxide, a highly engineered rust. In a large chemical reactor, we convert these nanoparticles to the right phase and elemental composition, the α ″–Fe 16 N 2 phase of iron nitride. This results in an isotropic powder, so we need to subsequently align all the individual magnetic moments of those individual nanoparticles and then compact them to high density.
Manufacturing permanent magnets from nanopowders has not been done before, so in many ways, we are inventing new physics and manufacturing methods along the way.
When you talk about this capability of creating thin films and nanomaterials, how much of that knowledge comes from the semiconductor world or other industries?
I think the semiconductor world has created revolutions from a materials and manufacturing perspective. It has brought an understanding and control of what happens at the nanoscale: from the physics that governs these regimes to the tools developed, both analytical and computational. We are very lucky, honestly, to have people coming from those industries and applying that rigor and quality control to our manufacturing and process. That knowledge and mindset are vital for us as we scale.
What’s exciting about the technology is not just making extraction and fabrication more sustainable but also how these magnets empower green tech and minimize the impact of other industries. Are rare earth-free magnets a climate solution, empowering other solutions, or a little bit of both?
Our solution can only have an impact when it’s actually used by our customers, our partners. If we just sit in our R&D labs and never make it to market, it’s a loss for all of us. Our customers refine the technology into a product, and that’s what gets us out of bed every morning. Working in the lab is nice, but out there in the world is where our magnets can really make a difference.
“We believe that the clean energy transition is necessary, but we have to be able to do that transition without creating other problems.”
And it sounds like you’re in this exciting stage, that transition from “We’ve made this thing, we know it works” to “How do we get it in the hands of as many people as possible?”
Exactly. Now it’s all about making it real, right? Making it happen. We’ve done the proof of concept, and it’s clear that the market is very interested in this product and this material, and there’s a strong need for it to support a more sustainable future for our planet, and to create a stable supply chain for powerful permanent magnets. Now, we have to make it happen, and we are.
Have you thought about these magnets’ role in a more circular economy?
Minimizing the environmental footprint of our magnets is very important to us, and getting as close as possible to a circular economy is our goal. Clean Earth Magnet is made from iron and nitrogen, and long term, it can be made from any iron source—scrap metal, literal rust, or even our magnets can serve again as a raw material input. Output gases from one part of the process can serve as inputs to other parts of our process. The manufacturing process can be designed to be circular, especially compared to the alternative, that it almost feels too good to be true.
Is there a Moore’s Law for magnets?
A Moore’s law for magnets likely does not exist. Magnetism is ultimately mainly based on the magnetic moment of orbiting electrons. Until we can engineer at this atomic scale, we’re kind of limited by the physics that governs the total magnetization of a material.
One thing that I would say, though, is that there’s still a lot of room for improvement in the performance of our Clean Earth Magnets. We’re not even close to the true potential of the α ″–Fe 16 N 2 phase of iron nitride, and that will come through further development and advanced processing capabilities. So, we’re not done yet, and we will keep going. The more magnetization that you can get out of a given amount of gram of material, the better, and we’ll keep pursuing that.
What will it look like if everything goes right for Niron? What does it mean for the company to execute its mission?
There are a lot of different applications where permanent magnets are used. Permanent magnets are in your phone, electromotors, and speakers; they’re in EV motors and wind turbines. The sooner we can get our product in the hands of our customers, the better.
The demand for permanent magnets is going to outpace current production, so, in a way, we owe it to the world to try to scale this technology as fast as we can. We can’t afford to let this technology sit on the shelf for 10 years, so it’s full speed ahead on getting it into the hands of customers. That’s what we’re executing right now.
It’s easy to imagine materials science and its future in terms of science fiction—nanomachines and Iron Man suits—but what does the future of materials look like?
This is such a difficult and interesting question. I can imagine that in the coming 20 years, AI will boost the materials sciences and engineering to a new level. It will allow us to design new materials more effectively by finding correlations between structural and elemental properties to physical properties. Manufacturing processes will become ever tighter through AI-supported process control. It will be exciting to see what the AI revolution will bring. There’s the potential that these new insights would leap-frog us into the next Materials Age.