Robots continue to evolve, out of the primordial factory floor, bravely taking on more complex, intricate tasks that previous generations would have floundered at. Spurred on by economic incentives for cost-saving and technological advancements, the reality of working with robots to enhance productivity and safety is here. While bipedal, humanoid robots may remain in the realm of science fiction, fully autonomous droids of all kinds are deployed in all sorts of settings.
Channeling the full potential of cutting-edge technology takes some doing, though. Particularly for robots, there are challenges pertaining to data; what kind of data to collect, how to store and access it, and how to engender trust between these sophisticated machines and the humans they support.
Growing into challenges and solutions
Robots have been around in the industrial context since the 1960s, improving productivity and enhancing safety. Despite being a mainstay on factory floors, robots didn’t make serious headway into nonindustrial settings until the COVID-19 pandemic. The global health crisis had a profound impact on what kinds of labor robots could do, and what humans should do.
“COVID actually was the major accelerator,” said Ofir Bar Levav, chief business officer of Indoor Robotics, a robotics company focused on security, safety, and maintenance inspections for indoor environments. “We talk about the four D’s of robotics: the dull, dirty, difficult, or dangerous jobs. People are not coming back to work, especially in those types of roles,” he said, “so companies are having a hard time recruiting and retaining workers.”
Simultaneously, technological advancements are pushing the limits of robotics. Powered by robust machine learning and talented engineers, robots are demonstrating remarkable progress in dynamic demonstrations. So, companies are seeing a confluence of economic incentives and technological capacity, driving rapid adoption.
“Compared to like two years ago, the level of acceptance of robotic solutions is much higher. Two years ago, people thought this was science fiction,” said Bar Levav. “Now they’re saying, ‘Yes, let’s implement and see how it works.’”
Robotics data collection and training
Like their autonomous vehicle cousins, robots are trained via huge datasets and machine learning, each simulation building on the last until the machine can deftly navigate its environment and complete tasks. This typically comes from running myriad tests and then iterating based on the data.
“Our robots are trained on thousands of cases, but when we get to a new site, more data is always better,” said Bar Levav. Indoor Robotics’ drones can collect up to 100MB/min while they run their fully autonomous missions. A fleet of global drones running missions can quickly add up. This data is invaluable for clients looking to protect their properties, as well as Indoor Robotics.
“The more examples we see of gas leaks, people, or thermal anomalies, the more we enrich the system,” Bar Levav said. “That not only enables our general systems to operate better but enhances the performance of our drones for that individual customer.”
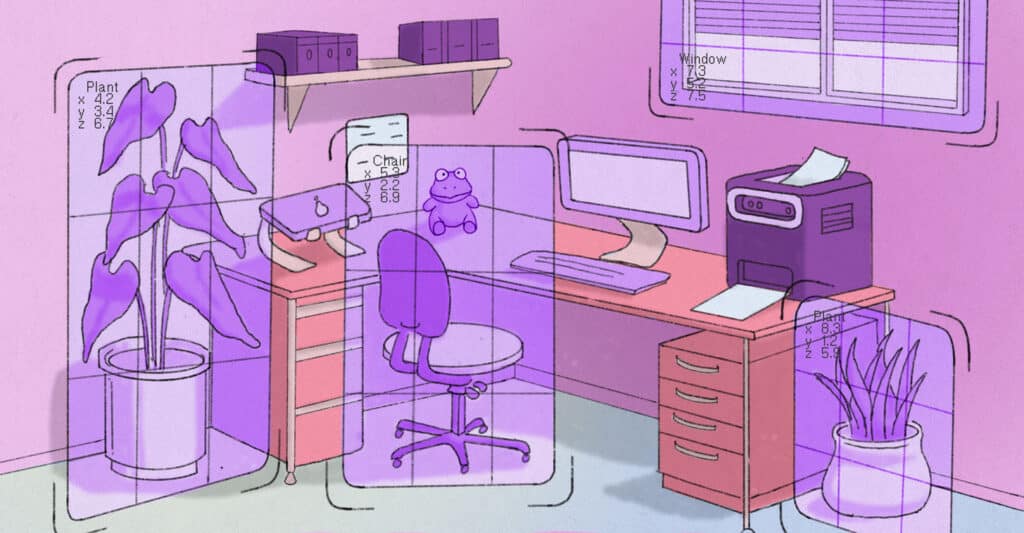
This kind of training is instructive but can be prohibitive for organizations looking to build their own solutions. For a company to create a bespoke robot to complete a unique task would require an immense amount of knowledge and engineering resources, out of reach for all but the largest companies. Luxonis, a spatial AI and computer vision platform, is focused on democratizing those resources and pushing robotics forward. The company bills itself as the eyes, ears, and brain of robots, offering hardware, software, and firmware solutions for robotics systems.
“Robots have been hard to deploy at scale for enterprises because there’s a lot of technology that needs to work together,” said Bradley Dillon, chief operating officer at Luxonis. “Luxonis was formed to make that process easy.”
Luxonis builds plug-and-play building blocks for computer vision and robotics. Sophisticated computer vision systems collect many gigabytes of data. The devices then leverage onboard computing to reduce that footage to mere kilobytes, streamlining data collection. This data is then available for analysis in RobotHub, Luxonis’s platform. From there, customers can control what data is collected, how long it’s stored, and more.
The company uses other technologies to break down barriers in robotics. Luxonis uses Unity, for example, to simulate prototypes. As opposed to physically building a robot to test, Luxonis uses the video game development platform to build and simulate tests. The data comes out perfectly annotated and is generated faster this way, cutting down on costs for customers.
The culminating effect? Luxonis helps get more robots into the world, which Dillon sees as a good thing.
“We really believe that there’s going to be all kinds of opportunities in robotics, and we’re trying to empower engineers,” Dillon said. “There are so often barriers that prevent you from learning, like a lack of data, and we want to lower that barrier, to provide an open playground for people to build and learn in.”
Fitting robots with flash
Robots, of course, come in all shapes and sizes, and finding a storage solution that works in a near-infinite number of situations can be difficult. Robots are constantly moving and interfacing with their environment and need to react quickly while collecting immense amounts of data.
“Flash storage is the preferred solution, thanks to its speed, small footprint, and a wide range of capacity points,” said Nadav Neufeld, a senior product marketing manager at Western Digital. “SSDs and embedded flash are the choice storage going into robots. Industrial and automotive-grade storage is often used to accommodate harsh environmental conditions.”
Additionally, as engineers train their stables of robots, failures can provide vital insight into what went wrong and how to improve. Resilient data storage is doubly important in these scenarios.
“Even [with] robots that are doing relatively simple missions, there are so many stimuli that need to be responded to. If something goes wrong, the machine needs to collect data for engineers to understand what went wrong,” said Neufeld, “like a black box of robotics.”
As such, the flash storage products that go inside robots must deliver high performance and high capacity.
Human-computer cohabitation
With any kind of data collection comes the omnipresent question of trust. A major challenge for robotics companies is earning the trust of people. First, the organizations and teams that work with robots need to learn to trust them.
“I think the challenges that we are seeing are more on the operational side. People are concerned that they have a robot flying in their office after hours,” said Bar Levav. “Is it going to crash into anything? Is it going to damage itself? I think that’s where we see people getting more comfortable because they see the technology maturing.”
Second, beyond the safety question, there are also questions of transparency and privacy. Clear protocols and communication over what data is collected, where it’s stored, and who has access to it are vital for building that trust. Luxonis gained firsthand experience with these challenges while building rae, an open-source robot aimed at placing cutting-edge robotics in consumers’ hands.
“With rae, everything is controlled by the app, but you can delete the data from a profile at any time,” said Dillon of Luxonis. “It’s about empowering users to feel confident that they control their data. That’s the key.”
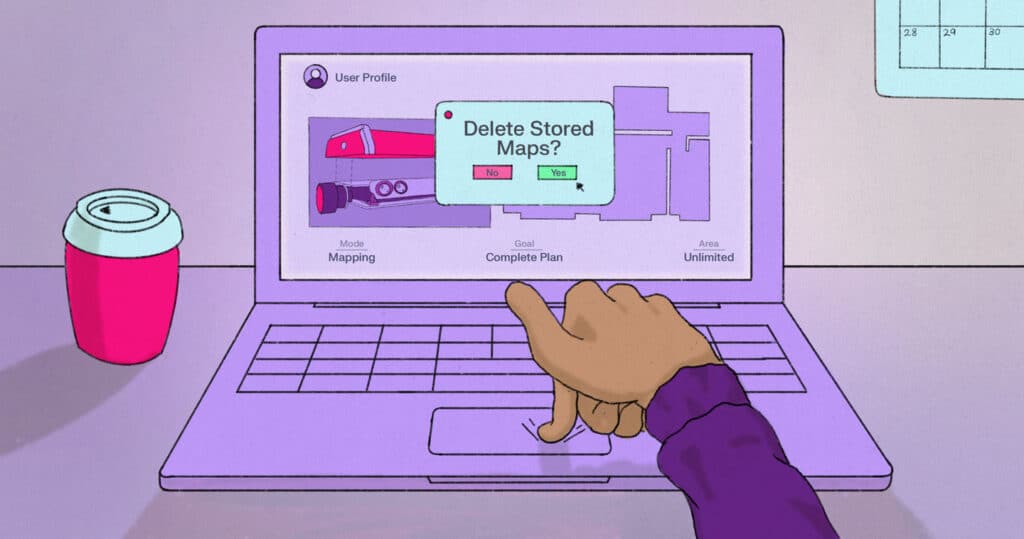
Beyond the human-computer interaction piece, which will continue to guide how robots interact with their human counterparts, there is a simple elegance in the adoption of these new tools. Because these processes are data-driven, more interactions with humans means more data to learn from. Robots, then, will get better at interacting with us, and humans will feel more at ease when they counter a robot in the wild.
The more time we spend together, the better we’ll get at being together. A happy feedback loop of cohabitation.