How Future Materials Will Define What’s Next
Human history has been defined by materials—the Stone Age, the Bronze Age, and the Iron Age. Materials serve as a measure of our progress, and new materials usher in transformative change. To explore what’s next, Western Digital talked with leading scientists and technologists about the possibilities of Future Materials. We live in an age where […]
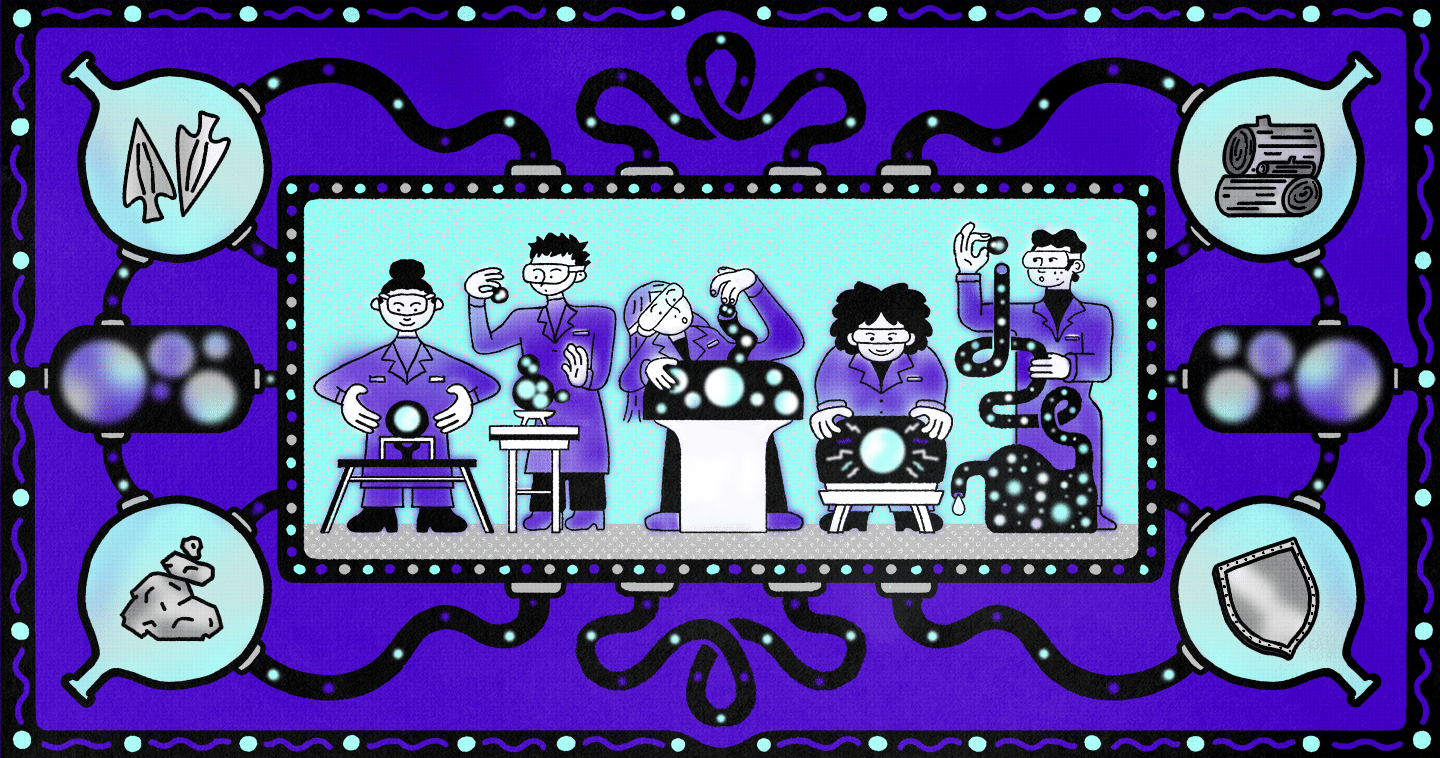
Human history has been defined by materials—the Stone Age, the Bronze Age, and the Iron Age. Materials serve as a measure of our progress, and new materials usher in transformative change. To explore what’s next, Western Digital talked with leading scientists and technologists about the possibilities of Future Materials.
We live in an age where technology and our understanding of the world are advancing at an unprecedented, exponential pace. Never before have humans had so much control over the materials that make up our world, but we are also reaching our limits. In the semiconductor world, for example, Moore’s Law is on a crash course with the laws of physics. In our relentless pursuit of progress and things, we are also reckoning with the finite nature of our resources and the impact of materials on our planet.
Tackling humanity’s most daunting challenges—from powering the energy transition to unlocking the potential of space and artificial intelligence—will require novel materials, technologies, and processes. To protect our future on this planet, and potentially our existence on others, requires rethinking even the smallest of details, at the atomic level.
A material world
Everything is made of something, so it’s hard to appreciate the mastery of materials our society has achieved. Many materials we take for granted, such as glass windows, are something we literally look through, while the knowledge we have gained of materials at the atomic level is something most of us can’t grasp.
“One of the reasons why our field feels intangible is that what we, materials scientists, are so interested in zooming in on the building blocks of matter,” said Dr. Anna Ploszajski, an award-winning materials scientist, storyteller, and author. “What we’re interested in is invisible.”
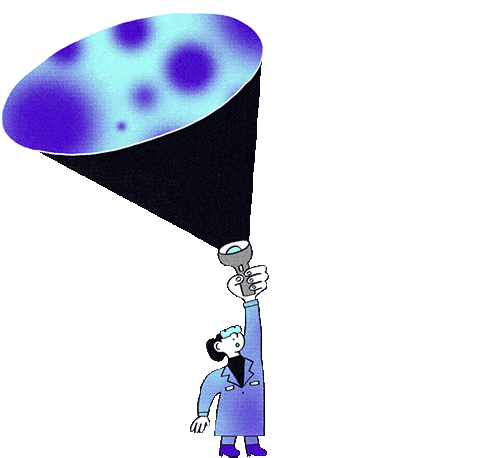
Yet from the beginning of our civilization, materials have defined us and our world.
“The story of materials is inextricably intertwined with the story of humanity,” said Ploszajski. “We measure progress by materials, and materials and our current technologies say everything about us—about what’s important to us, about our attitudes.”
Ploszajski’s post-doctoral research focused on smart materials and 4D manufacturing platforms—substances that respond to changes in their environment, with the fourth dimension being time.
“Instead of programming or creating robotic actuators, materials can inherently respond to their environment, like shrink or expand,” she said. Her favorite example is the pinecone and how it opens or closes its scales in response to changes in humidity. Similar mechanisms, she said, are researched in creating materials for self-deploying structures.
Ploszajski is part of a burgeoning movement exploring biomimicry, an approach to innovation inspired by nature’s designs and processes. Over eons, evolution fashions biotic and abiotic systems into efficient and resilient systems. Our human brains, for example, are capable of processing information with the energy equivalent to a modest light bulb. Computer engineers are hoping that new materials will help them to mimic the brain through neuromorphic signal processing, and unlock a transformative change for computing.
Recently, Ploszajski shifted from her work in research to storytelling. An author and podcast host, she’s trying to bridge our understanding between where our stuff comes from—the physical atoms and how materials get processed—and how they form the objects that make up our daily lives.
The cost of doing things the same
“Our objects say everything about us, but they come at a cost,” she said. “All of our stuff comes at a cost—an impact on the planet. So, it’s a bit of an interrogation to ourselves about the things we can’t live without. What cost do these objects, do our modern lives, have on the planet? And what are we willing to pay?”
High-performance magnets are among the many obscure technologies our digital lives rely on. These strong magnets, powering countless electronic devices, are made possible by rare-earth metals, most notably neodymium and samarium cobalt.
The environmental cost of mining and refining these materials is far from abstract, though. For every ton of rare-earth elements, 2,000 tons of highly toxic waste—dust, gas, and radioactive residue—is generated.
However, these magnets are not only part of countless electronics. Their powerful magnetism is also what helps turn motion into electricity, making them the backbone of electric vehicle motors and wind turbines. The imminent energy transition is causing a soaring demand for these magnets, but their environmentally taxing processes make it difficult to keep up with demand and undermine their green benefits.
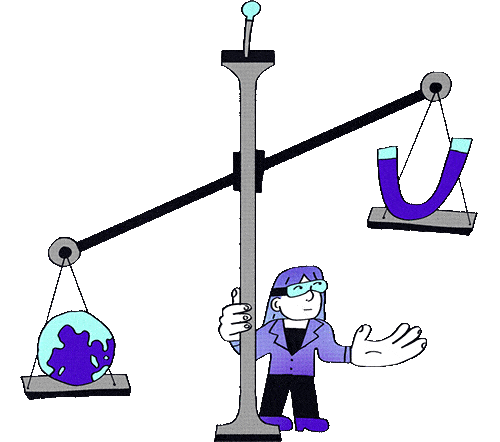
“We don’t want to replace one ‘evil’ with another, right?” said Carlijn Mulder, the scientist leading the R&D department at Niron Magnetics. The US startup is producing the world’s first commercial Clean Earth Magnet®, a powerful, permanent magnet made without rare-earth elements thanks to a materials breakthrough: the α ″–Fe 16 N 2 phase of iron nitride.
“If we can manufacture these high-performance magnets with abundant materials, with a clean process, that’s going to be huge for the future we’re all pushing towards,” she said. “We believe that the clean energy transition is necessary, but we have to be able to do that transition without creating other problems.”
Despite its difficult nomenclature, there’s a lot to get excited about the potential of permanent magnets made of α ″–Fe 16 N 2. Scientists have shown that, theoretically, the material can achieve 50% higher magnetization than rare-earth magnets. And it can be fashioned with some of the most abundant and easily accessible elements on our planet.
“We believe that the clean energy transition is necessary, but we have to be able to do that transition without creating other problems.”
“The Clean Earth Magnet® is made from iron and nitrogen, and long-term, it can be made from any iron source—scrap metal or literal rust, and Niron’s magnets can even serve again as a raw material input,” said Mulder. “Output gases from one part of the process can serve as inputs to other parts of our process. The manufacturing process can be designed to be circular, especially compared to the alternative.”
Hopefully, it isn’t. But achieving reliable bulk production of a material made from the ground up is a formidable challenge. Mulder and her team are relying on learnings from the semiconductor industry—from understanding materials’ underlying physics to the rigors of manufacturing quality process controls at scale. It’s a pioneering effort.
“Manufacturing permanent magnets from nano-powders has not been done before, so in many ways, we are inventing new physics and manufacturing methods along the way,” said Mulder. “We owe it to the world to try to scale this technology as fast as we can. We can’t afford to let this technology sit on the shelf for 10 years.”
A petajoule challenge
We like to think of progress as a simple, linear process. But the truth is that a breakthrough like Niron’s magnets relies on decades of scientific research. Most technologies undergo a long journey between initial material discovery and a product we can hold in our hands.
Lithium-ion batteries are one of those revolutionary technologies that spanned decades of research. It’s hard to imagine our world without them. They enable portable electronics, electric mobility, and they make solar energy a viable alternative to fossil fuels.
Yet lithium-ion batteries are reaching their limits, explained Dr. Y. Shirley Meng, one of the world’s leading experts in nanomaterials for energy storage, professor at the Pritzker School of Molecular Engineering at the University of Chicago, and chief scientist for Argonne Collaborative Center for Energy Storage Science.
Today, explained Meng, we are producing only about two terawatt-hours of batteries per year (a terawatt-hour is just about enough to power the United States for an hour). But electrifying the world will require about 200 to 300 terawatt-hours of battery capacity.
“If we want to build so many gigawatt factories, we’re going to run out of cheap lithium, we’ll run out of nickel, and out of copper,” said Meng.
Meng and her team are working on a plethora of alternative battery materials—sodium-ion, lithium-metal, lithium-sulfur, and solid-state batteries. She sees them all as viable and necessary battery contenders.
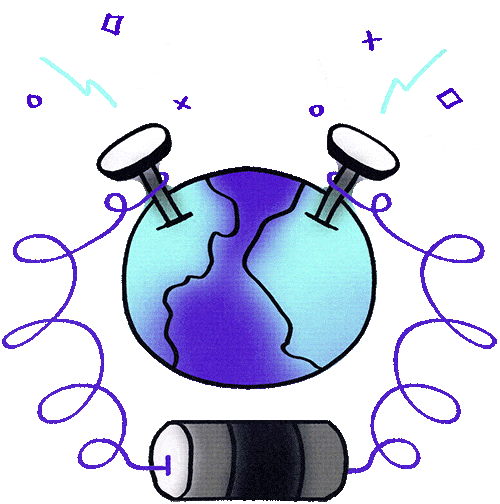
“If you ask me which technology will succeed, in my opinion, all of them have to succeed, every single one of them,” she said.
For Meng, the future of batteries will rely on three major breakthroughs. The first is the materials themselves—finding plentiful, easy-to-access materials, and using them in perpetuity.
“The semiconductor industry could be sustained so well because we have silicon, right?” she said. “So when we look for materials, the number one thing is the geology tables. Do we have enough and can I scale to a terawatt hour, to a petajoule?”
Relatedly, Meng emphasizes that we must learn to use materials with circularity, so their resiliency is key.
“How can we sustainably make those battery-active materials—nickel, cobalt, lithium, sodium—and then be able to recycle them?” she said. “Once you take it out from the mines, they will circulate in the world in perpetuity.”
The second is about unlocking capabilities at the nano-level.
“We know things behave differently in the nanoscale compared to the bulk, and we can actually access the unique capability of materials when we control them and place them in the right position at a molecular level,” she said. “The biggest challenge is how do you use these properties billions of times, with the same accuracy and the same precision.”
But the final breakthrough is less about the technology and more about a fundamental shift in thinking for the industry and our society.
“For the energy transition, the picture is that the whole infrastructure must change,” she said. “The mindset has to be that batteries are infrastructure, not disposable.”
Space materials
Speaking to a multitude of scientists, it becomes clear just how vital energy is in the quest for new materials. While much of the focus has been on finding clever ways to use our planet’s resources and mechanisms, scientists have always looked to the stars for inspiration.
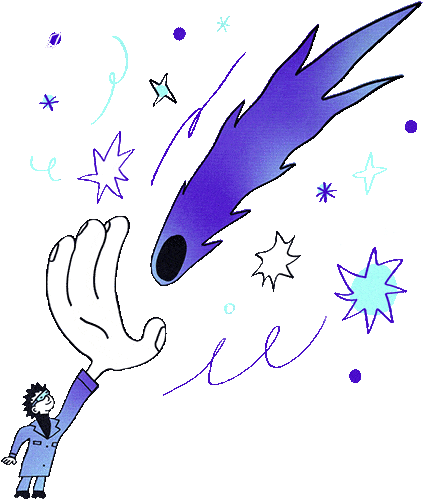
One of the concepts that has gained momentum as a zero-emissions engine is space-based solar power. While capturing solar power in space and transmitting it wirelessly to Earth is a pretty sci-fi concept, the technology has recently made headlines as a feasible undertaking for the next few decades.
But building these mega structures requires materials that we don’t possess yet, explained Bianca Cefalo, the CEO and co-founder of Space DOTS—a startup enabling easy access to materials testing in space.
“Beside the technological challenge of generating power beamed to Earth from kilometers away, is the massive number of structures that need to be deployed into orbit,” said Cefalo.
“First, it’s not going to be deployed in the usual low Earth orbit, because it requires different positioning. Then it needs solar panels that are kilometers long, that we need to figure out a way to send, deploy, and assemble in space, and we need manufacturing techniques and materials that are commercialized and strong enough to resist more than 30 years in the same position while remaining functional. These materials don’t exist. They are not commercially available yet. So, it’s complicated. It’s difficult and we will need a lot of trials (and time) to get this right.”
Cefalo, who served as a fluid-dynamic engineer on the 2013 NASA/JPL Insight Mars mission and is a former Airbus Defense and Space thermal product manager, hopes her company can make those trials happen often and fast.
Space DOTS developed a smartphone-sized materials lab that can hitch a ride on existing satellites. Instead of simulating the conditions of space by using multiple, fancy machines on Earth, materials can be tested in space, delivering more accurate results about how they will react structurally to the cumulative effects of vacuum, radiation, solar flares, and atomic oxygen.
“Around 90% of the spacecraft and satellites in orbit today, are made out of aluminum alloys that we have used since the Apollo mission in the sixties!” she said. “But now with an ecosystem growing at an exponential rate and projected to reach $1 trillion by the year 2040, everything sent into space, down to the very tiniest patch of glue, is a novel materials challenge and a potential new business opportunity.”
With launches now a near-everyday norm—212 successful launches last year alone—Cefalo emphasizes that the industry is moving toward far more extraordinary challenges.
“Everything sent into space, down to the very tiniest patch of glue, is a novel materials challenge and a potential new business opportunity.”
“We’re amid a huge shift where the entire space industry is moving past rockets and satellites toward ambitious programs like commercial space stations, space travel, in-space manufacturing, space-based solar power stations, asteroid mining, and human habitats around the Earth and on interplanetary soil,” she said. “So, there is a need for new materials that are lightweight, enhance performance, and are easy to commercialize in less than 10 years.”
If we think about all we have achieved on Earth, Cefalo is hoping to help find the materials to replicate all that, and more, in space. But she’s even more hopeful that extraterrestrial materials will become a means for improving life on Earth.
“We’ve seen how the production of materials in orbit can produce stronger alloys and more efficient crystal structures that contribute to more effective semiconductors or advanced pharmaceuticals,” she said. “At the same time, metals like rare-earth elements, could be extracted from celestial bodies. It’s very far away. It’s sci-fi, but this is where I hope we are heading.”
But getting to those materials, building the machines that can extract them, finding ways to recycle space debris or manufacture in orbit, will rely on a sparce space resource—data.
“It is fair to say that human knowledge about the environment of space is extremely limited,” said Cefalo. “The farther we move from the low Earth orbit, to Cis-lunar for instance, the less we know how the environment impacts space systems. The reality is that the simulation models and ground testing facilities used by the industry to develop space systems are calibrated and tuned on a massive guesstimate. But we need data to accurately replicate conditions in these places if we want to design systems that are reliable, resilient, and safe.”
When AI came marching in
Back on Earth, the wealth of data we have accumulated about terrestrial materials is astounding.
“Silicon is probably the most researched material in human history,” said Derek Stewart, senior technologist and resident theorist in Western Digital’s R&D, exploring future non-volatile memory technology.
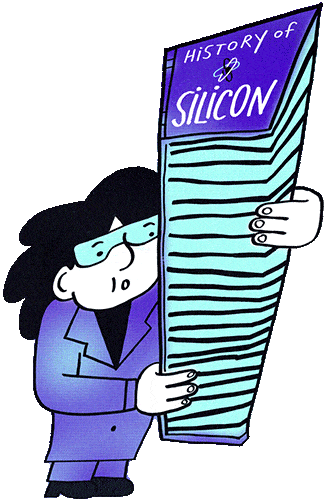
“We [human civilization] know quite a bit about materials,” he continued. “We’re at the point where we can construct devices that are a combination of deposited nanoscale material layers, some just angstroms thick, and it’s fairly routine.”
Stewart’s career in the semiconductor industry put him in a front-row seat to the frontier of materials science. But computing, and processors in particular, has come to an interesting crossroads, reaching the physical limits of how far devices can shrink. Instead of continuing on the Moore’s Law highway, hardware is transforming into differentiated devices, finely tailored to the workloads it supports.
“We need to kind of expand and diversify and evolve to address specific initiatives and problems like neuromorphic computing,” said Stewart, “and new materials may be more important in tackling this.”
Material breakthroughs have always been a driving force in advancing computing power, increasing memory capacity, and sustaining the clip of Moore’s Law. Now, computational capabilities are helping to advance materials discovery for future devices.
“This a golden age for computational materials science,” said Stewart. “There is a convergence of cheap, fast computers with large memory capacity, robust theoretical approaches like density functional theory, and the introduction of efficient parallel computing algorithms that can tackle quantum-mechanical calculations—a perfect confluence for large-scale computational materials searches.”
One of the biggest contenders for breakthrough change in advancing the material world is AI. Already today, scientists are using AI to tackle the most tantalizing ideas for near-limitless sources of clean energy, like fusion energy and room-temperature superconductors. And AI models have identified millions of new crystals and stable materials that could power future computer chips or solar panels—a discovery that would have taken humans 800 years to arrive at.
For Stewart, a seasoned veteran in the journey from discovery to product, it’s an exciting time but not one he’s celebrating quite yet.
“I think we should be cautiously optimistic,” he said. “We need to view these searches as another tool to identify promising areas for future exploration. But it’s also important to note that a lot of these materials do not exist in nature, and it can take time to either verify or disprove these theoretical predictions. It’s not going to solve all of society’s problems tomorrow, but it is informing new materials areas to explore.”
And until AI helps scientists crack the code on clean energy, it will serve as a double-edged sword. AI workloads have become so pervasive and energy thirsty, they are creating an unprecedented surge in demand, one where our energy systems may struggle to cope.
A materials shift
If materials science has long been considered the forecaster of technological advancement, these five scientists point to a major shift into an era marked by environmental concern and resource constraints.
“Our future material world will look different,” said Anna Ploszajski. “Rather than creating ever more complex devices, machines, and objects out of new materials or old materials that are then impossible to repair, impossible to recycle, impossible to do anything with after they break, it’s about finding more simple designs using fewer materials to achieve the same results.”
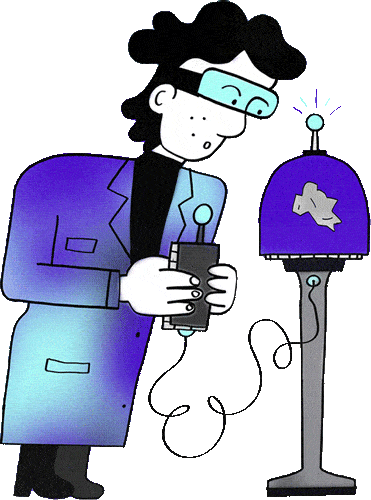
If history has been defined by materials—the Stone Age, the Bronze Age, and Iron Age—our current age is best described by the innumerable plastics that suffuse our world and the silicon powering the Information Age.
The future, however, may not be marked by materials that propel us, but rather by those that limit us. Sustaining our future on a dangerously warming planet, and one orbited by a growing mass of space debris, will be about working around materials as much as working with them.
“Carbon is the kind of thundercloud on the horizon,” said Ploszajski. “I’d be surprised if carbon isn’t the material to define the next age for us. It is the turning point for humanity.”
For Ploszajski, Mulder, Meng, Cefalo, and Stewart, future materials will be made possible by nanoscale engineering, AI, and the accessibility of space, but it will be defined by our ability to reconcile technological progress with environmental sustainability.
“The difference for future materials will be between a circular materials economy and not,” said Ploszajski. “A circular materials economy is sort of counter to how a lot of our material world has progressed so far, because we’ve been striving for increased complexity. But a more sophisticated approach will be in engineering elegant and efficient uses of materials and how we deploy them.”
Credits
Editor and co-author Ronni Shendar Research and co-author Thomas Ebrahimi Art direction and design Natalia Pambid Illustration Cat Tervo Design Rachel Garcera Content design Kirby Stuart Social media manager Ef Rodriguez Copywriting Miriam Lapis Copywriting Michelle Luong Copywriting Marisa Miller Editor-in-Chief Owen Lystrup