When Western Digital expanded its hard drive manufacturing site in Thailand, the first time the assembly lines were turned on wasn’t on the factory floor; it was on a laptop 8,000 miles away.
Before any physical machinery found its place within the newly constructed walls, teams of engineers meticulously crafted its virtual counterpart. This digital twin could mimic the operations down to every tool, robot arm, and even the pace of human operators, flawlessly simulating the assembly of the company’s most advanced enterprise hard drives. Engineers could quickly test different layouts and operation scenarios without touching the production line.
While simulation has long been a staple in manufacturing, the concept of digital twins is a different paradigm, explained Suraj Rao, vice president of Western Digital’s advanced analytics office.
Rao shared a simple example: In traditional simulation, optimizing a bank’s queue times focuses on mathematically parametrizing the distribution of customers in relation to the number of agents and available teller counters. A digital twin, however, would go further. It will replicate the physical layout of the bank to understand not just how many people use it, but how they use it; the flow of customers inside the bank.
“You’re trying to mimic the actual physical process to include constraints that may not be captured in a mathematical model,” said Rao. “While your mathematical model may point you to add another bank teller counter, the digital twin may show you that adding another counter will only cause overcrowding, and that the better solution is to incentivize customers to come at different hours to equalize the load.”
A factory in the metaverse
Simulating a bank queue is one thing; replicating one of the world’s most advanced factories is another. Designing the digital twin of Western Digital’s new manufacturing building required collaboration among industrial engineers, manufacturing engineers, test engineers, and operators to bring together the complex data needed to mimic operations.
Putting all those details into code was Laszlo Lenart, a principal engineer in Western Digital’s advanced analytics office, who meticulously coded the digital twin’s thousands of parameters and their possible combinations.
“One part that makes this model complex is the production itself—hundreds of components and processes need to be executed to make a single hard drive,” said Lenart. “The other part is the model size and all the moving units in the model. It’s a complete material flow starting from the stocking area through component assembly, hundreds of thousands of tester racks, and all the way until shipment.”
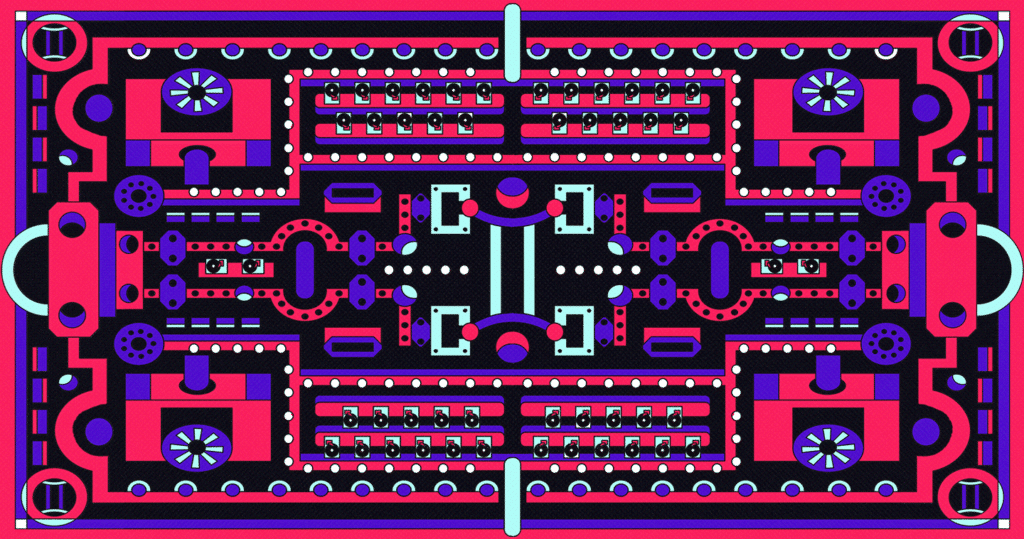
Lenart’s simulation runs millions of units—machines, components, assemblies, robots, carts, and even operators. Watching his laptop screen is akin to observing a complex game of Pac-Man. Objects flow seamlessly through narrow corridors of the simulated assembly line, never colliding, orchestrated in perfect harmony.
For engineers, this digital replica was a sandbox of creativity. Traditionally, the manufacturing industry adhered to an “if it works, don’t touch it” philosophy, fearing that alterations might introduce unforeseen risks, explained Lenart’s manager, David Gyulai, director of advanced analytics at Western Digital.
“But when you simulate a whole factory on your laptop,” said Gyulai, “you can try any crazy idea. You can try to find potential ways of doing things differently, explore what-if scenarios, and even radical ideas can be safely carried out.”
The caveat, of course, is that each of the meticulously coded data units must be impeccable to yield true-to-life results.
It’s all in the data
Lenart, originally from Hungary but now based in the U.S., has never set foot inside the yet-to-be-built factory; nor has he seen its future physical tools. His entire simulation depended on getting data from his companions in the company’s factories across the globe.
“A key part of simulation modeling is the critical thinking, asking the right questions,” he said. “A simulation can only be complete if you ask everything relevant, and, if you get the right answers.”
Gyulai concurs. “Simulation is very data hungry, so it can really be garbage in, garbage out,” he said. “You can have a good model, but if your data is trash, the results will be trash.”
On the hunt for the “right” data was Rutsamee Sanguanpong, the advanced analytics office’s program manager in Western Digital’s Thailand HDD operations. With each question Lenart posed, Sanguanpong had to uncover its answer with factory subject matter experts.
“Our challenge was that we had to build everything from scratch,” she said. “There were no physical machines to go to, and we needed to simulate new machines that are different than our existing assembly line.”
For most projects, Sanguanpong could go into the factory and measure parameters like cycle times, yield, output, or level of automation. Here, she needed to extrapolate data from experts about machines and processes that had yet to materialize.
“Because there is no physical operation in the building, we [the advanced analytics team] needed to validate our findings with the subject matter experts, making sure our simulation model fit the expected action,” she said.
Data needed to constantly flow in and out of the model, relying not only on algorithms but on the capacities of human communication and imagination.
Driving autonomy
One of the standout achievements within the virtual-turned-real factory was the automation of assembly through Automated Guided Vehicles (AGVs) because they could significantly reduce the need for human intervention in the assembly process. Minimizing human intervention reduces the risk of contamination, improving hard drive quality, explained Hisashi Itou, senior manager of manufacturing engineering at Western Digital, whose team designs the assembly tools in the factory.
“In addition,” said Itou, “manual handling and manual transportation create an amount of shock that can risk very sensitive components, such as the ultra-precise positioning of the head stack assembly.”
But to realize the project in the factory, Itou and his team needed to develop new physical mechanisms that would allow the AGVs to autonomously load materials into machines. Each idea required a dedicated virtual counterpart—one tool may require five components while the next a thousand.
More than 20 engineers provided data and concepts to Sanguanpong and Lenart. Lenart’s simulation was like a living organism, changing and growing with parameters and ideas every day.
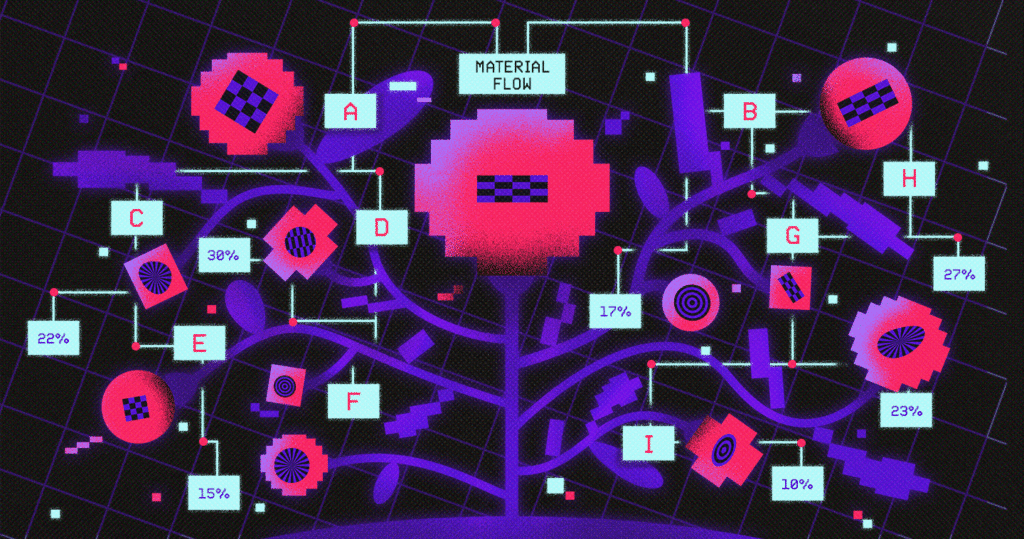
Within a few months, the teams designed a refined material flow based on the optimal number of machines, boosting production output by 15% and reducing cycle times by 10%. And like the bank queue, the simulation could recommend an optimal number of AGVs and their routing logic—the “just enough” model that can maximize efficiency and avoid robot traffic jams with the least capital expenditure.
“What we did would be impossible to simulate without a digital twin,” said Itou.
The human touch
For Rao, who has been overseeing many of the company’s data-led Industrial 4.0 projects like digital twins, the speed of adoption over the last few years has been astonishing.
“Once the technology [digital twin] was showcased, factory leaders realized there is a very low-cost approach for evaluating business options in a factory environment,” he said. “You can play with all the knobs on this distant virtual system which mimics the factory, and you can rule out a bunch of things that you shouldn’t be doing.”
Rao admitted that at first, he was surprised by the pace of adoption, but in hindsight, it was obvious. “It’s a low-risk approach to get things right, which is uncommon in manufacturing,” he said.
But his main takeaway from the success is that it’s still not easy.
“There is a natural barrier in terms of the availability of data,” said Rao. “Then there’s the availability of the right business process to support it, and of course, the challenges of the technology solution itself. But it’s mostly hard because the skill that is needed is in short supply.”
Gyulai, who has been building out the team of digital twin experts, concurred. “Processes are very hard to capture because operations are very dynamic. You need people who can drill down to the details,” he said.
“It all comes down to the right data, subject matter expertise, teamwork, and human intuition.”
Artwork by Cat Tervo